How To Series: About - Resistors & Potentiometers
|
Peter Lankshear, Invercargill, New Zealand. photos coming soon...
[
Safety
|
Basics
|
Transformers
|
Speakers
|
Coils IF & RF
|
Capacitors
|
Resistors
& Pots |
Valves
]
Also check our resistor data pages out
Resistors -
second only to capacitors, are the most frequently encountered
components in receivers. There are two families in general use, wire
wound, and the group known as carbon, each category having both fixed
and variable forms. Whilst there are overlapping areas, the two types
have separate functions. Wire wound resistors are the more expensive and
are used in high current conditions or where high stability is required.
It is rare to find them with values above about 50k.ohms, and some
manufactures avoided them where possible. Carbon resistors are the
mainstay of any receiver and can cover the whole spectrum of values.
As well as being made from carbon and an inert binder such as clay.
"carbon" resistors can also be composition, carbon film or metallized.
Whilst these have their specialist uses. In standard valve radios the
various categories can be regarded as interchangeable which is just as
well, because they can be hard to differentiate.
Carbon resistors do not have long-term stability, particularly if
operating near the1r full rating. Even “new” unused resistors will be
often found to have increased in value. Most likely to have changed in
operation are voltage dividers and audio amplifier anode and screen grid
dropping resistors. Tolerance should be taken into account when checking
values. Resistors with a gold band or end have a 5% tolerance. 10% types
have a silver coding whilst no tolerance code means that a variation of
up to plus or minus 20% of the marked value can be expected. Thus a
nominal 1000 ohm resistor con be as low as 800 ohms or as high as 1200
ohms, which is quite a large variation.
Radial leads were favored in early resistors. The resistive element was
much like an overgrown pencil lead, often encased in a ceramic tube,
some having cast metal ends. Receivers of U.S. and local origin used
resistors coded in the standard R.M.A. colors whilst the Europeans
favored printing the value on the body. Philips had an annoying habit
of labeling only with a part number. Unless you have a circuit or parts
list, checking values of these resistors can be very frustrating.
Fortunately, Philips has always made very good resistors and if
electrode voltages seem right, don't worry too much.
In the mid 1930's insulated molded resistors with axial leads became
common although their reliability did not improve much. Around this time
there was a gradual change from the "body-end-dot" coding to bands of
color. Atwater Kent were characteristically reluctant to join in the
R.M.A. coding system and often used their own peculiar code. In European
radios, resistor values were often printed on the body.
Whilst carbon resistors can change value even when unused, the commonest
reason for their being out of specification is over rating. This results
from resistor manufacturers being over optimistic about the long-term
stability of their products, particularly with high value, low wattage
types. Ohms law says that a 250k anode-coupling resistor may be
dissipating 0.1 watts, but experience has shown that commonly used 0.25
watt resistors. often fail in this situation. Carbon resistors in the
10k -25k range used for supplying R.F. valves are often operated at
maximum ratings and are likely to have increased in value. Conversely,
when subjected to heavy overload, very low value carbon stick resistors
can decrease in value, probably because the binder carbonizes.
A good indicator of resistor problems is a set of voltage readings, but
these must not be taken as the last word, one way or the other. Other
faults can upset voltages and it is quite possible for voltages to be
correct although resistors can be defective. Care is necessary in
checking and interpreting measurements of resistors. As a generalization,
a resistor should be disconnected at one end before it is measured. If
there is no D.C. path beyond the resistor, typical examples being anode
and grid resistors, it can be tested in circuit, but if there is any
doubt, disconnect it before testing. The high value resistors most
likely to be out of specification are the audio amplifier anode coupling
and where used, the audio amplifier screen resistors. Today, resistors
are cheap and plentiful and if there is any doubt, the easiest approach
is to replace anyway. Modern 1 watt resistors are small enough to be
fitted just about anywhere in a valve radio, so to avoid doubts or
uncertainty about ratings, I recommend using them for replacement
universally.
Wire wound resistors are made with resistance wire wound on to a former,
often ceramic, and the assembly is frequently encased in a vitreous or
molded coating. Taps are often fitted and occasionally these are
adjustable. Others, particularly HT voltage dividers, are encased in a
tinned metal strip casing- with protruding tags for connections and tie
-points. Known as “candohms”, an appropriate pun, they are an excellent
idea that didn't quite make it. Unfortunately, they are notoriously
unreliable and frequently are found to be open circuited in one-or more
sections. It is quite likely that, as a result of previous servicing,
there will be other resistors already bridging a defective section.
Another type of wire wound voltage divider will often be found
in-Australian receivers. These are made from a cardboard or fiber former
an inch or so in diameter with adjustable clips for the tappings.
Unfortunately, these voltage dividers are another good idea that didn't
quite live up to expectation. The slightest heavy handedness in
adjusting or tightening the taps is likely to break the fine resistance
wire and there is no reliable way of mending it. Years of operation can
oxidize taps and make contact with the element unreliable. The accepted
way of servicing voltage divider assemblies is to bridge the defective
section with a new resistor. If the resistance of the section is known
there is no problem. However, if this is not the case, a bit of common
sense and experimentation may be necessary. It is possible to derive the
exact value by calculation but there are so many variables that giving
an easy or foolproof formula is not practicable. Wire wound resistors
are used in high wattage situations and they therefore get hot, so watch
that they are not mounted close to other components.
Before 1940, some manufacturers used flexible resistors. These were made
by winding thin resistance wire on a string or asbestos core and
covering it overall with cotton braid. Apart from some sort of
termination, these resistors looked like a length of wire and can be a
trap for the unsuspecting. What appears to be an innocent piece of
hookup wire can produce a voltage drop, or even be open circuited!
Potentiometers
The term potentiometer correctly refers to a bridge type of voltage
measuring instrument, or potential meter, and usually found only in
laboratories. It operates as a bridge, comparing an unknown voltage
against a reference voltage. A variable resistor is adjusted to give a
null on a meter and the unknown voltage is calculated from the ratios of
the two sections of the resistor, which form a potential divider. As a
volume control can be regarded as a potential divider, the association
with the laboratory instrument is understandable. The term stuck and
although true potentiometers use slider adjustments, the term “pot”- has
come to mean in general, high value variable resistors for volume and
tone controls in receivers.
The earliest receivers had no volume control. Valve gain was controlled
by the adjustment of valve filament current with a low value variable
resistor, frequently called a rheostat. Later, with the advent of
indirectly heated valves, control changed to varying the cathode bias of
R.F. amplifier stages. By the mid 1930's, diode detection and automatic
gain control were being very widely used. The associated volume control
was a high value variable potential divider controlling the audio signal
from the detector, and thus the familiar “pot.” came into general use.
Tone controls use the same type of pot, with elements made of carbon or
related compounds. Mechanical and physical arrangements vary with each
manufacturer. The resistive element may be molded or simply coated on
to a cardboard base. Moving contacts may be anything from wiping arms to
plates pressed onto the resistive strip by rollers.
Being electromechanical devices, volume controls are prone to problems.
The two major troubles are wear and dirt. Both show up as dead spots and
noisy scratchy operation. Replacement is the only real answer to wear.
An aerosol cleaner can sometimes deal with dirt, but, unfortunately, the
cure is all too often temporary. Again, replacement is the only complete
remedy. Fortunately, the great majority of valve radio manufacturers
used the industry standard 3/8 inch diameter-mounting bush with 1/4 inch
shaft, and replacements are still generally available. One manufacturer
has not been helpful however. The Philips organization used very special
controls that were different. Restorers are on their own with
cannibalization one option.
Standard values for volume controls can vary anywhere between 250 k.ohms
arid 2.0 megohrns, with 500 k.ohms being typical. Choice of the exact
value and circuit configuration is a design trade off in a surprisingly
complex situation. Normally the volume control forms part of the diode
load, either directly or connected via a coupling capacitor. The
resistance following the coupling capacitor should be at least twice
that of the diode load resistor if distortion is to be kept low at high
modulation levels, and some manufacturers did not always observe this
requirement. Electrically, the best position is for the volume control
to be the diode load itself but, because the diode current will then
flow through the control, noise is much more of a problem. All this is
to say that. To be safe, a replacement should have the same value as the
original.
An important characteristic is the resistance taper of the replacement.
Volume controls do not have a uniform variation in resistance throughout
the length of the element. The reason for this lies in the
characteristics of the ear. Nature has decreed that sound intensities
can vary in power by a factor of at least 100 million to one (80 db).
The only way that ears can handle such an enormous range is for them to
be very non-linear in volume sensing. For the mathematically inclined,
the response of the ear is logarithmic and consequently the unit of
sound level relationships is a logarithmically based unit, the decibel
(dab). Volume controls therefore have something approaching a
logarithmic taper.
I haven't the space for more detail, but logarithms are dealt with in
any secondary school maths textbook. Obviously, then, linear taper
potentiometers are not suitable for volume controls. There is little
standardisation in markings indicating the taper. Some are clearly
marked NLOGN while others have a letter, or A for log, and B for linear.
C may indicate a reverse taper (fortunately not commonly found in
receivers). There is a simple way to identify the characteristics. Set
the rotor to the half way point and measure the resistance of each outer
terminal to the centre. A linear control will have equal halves whilst a
log control will have somewhere between 10% and 25 of the total
resistance in the lower section.
Many volume controls have an extra terminal connected to a resistor and
capacitor. This network is des1gned to boost the bass response at low
volume settings. Again, this is to compensate for the characteristics of
the ear, which at low sound levels suffers a loss of low frequency
sensitivity. New tapped controls are hard to find now and the only
practical method is to ignore the network and use a standard control for
replacement.
Two types of tone control were in general use. Most common was a simple
capacitor and variable resistor combination connected between the anode
of the output valve and either HT or earth. Progressively more high
audio frequencies are bypassed as the control is adjusted towards
minimum value. Tone controls were generally about 50 k.ohms. The
capacitor, often about 0.05 mfd can be subject to a lot of stress and it
is possible for them to short circuit resulting in a burned out control.
Some later receivers used the more sophisticated negative feedback type
of tone control in which typically, a 0.5 megohm pot. controlled voltage
fed through a small value capacitor connecting the output stage anode to
the anode of the driver- stage or grid of the output valve.
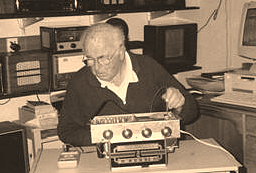
|
|